Operational efficiency is crucial in manufacturing, yet outdated paper-based processes might silently drain your profits. Every day, these hidden inefficiencies could be costing you more than you realize. To stay competitive and boost your bottom line, it's essential to identify and eliminate these outdated practices. Here are five ways paperwork could undermine your operations, along with steps to fix them.
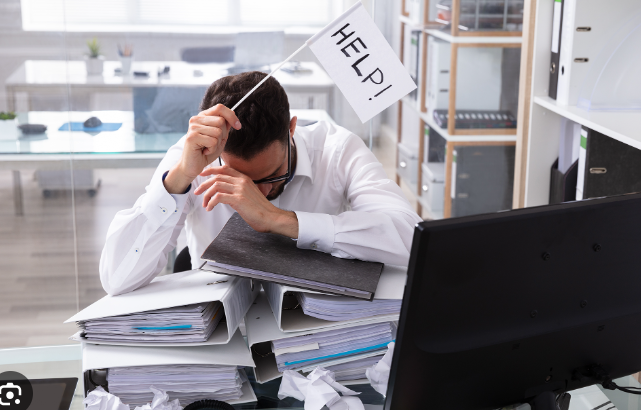
1. Time Wastage in Production and Administration
Problem: Relying on paper-based procedures is a time-consuming bottleneck, slowing down everything from inventory tracking to job assignments, and causing costly delays.
Impact: In manufacturing, every minute wasted on administrative tasks like filling out forms, searching for documents, or waiting for approvals isn't just lost time-it's lost revenue. Did you know that inefficiencies such as manual paperwork can drain 20-30% of your yearly revenue, according to the International Data Corporation (IDC).
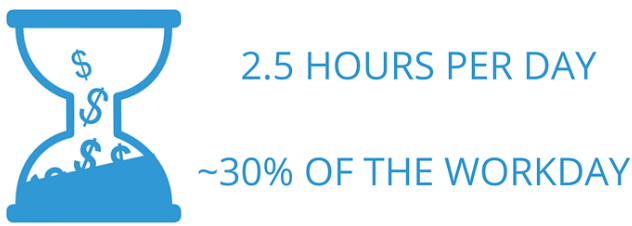
Solution: Imagine cutting down on tedious paperwork and boosting productivity by going digital. A streamlined document management system (DMS) can significantly reduce the time spent on administrative tasks with quick search and retrieval algorithms.
PwC estimates employees spend up to 40% of their time searching for information. By digitizing, you can reclaim that time and redirect it towards advancing your business.
2. Increased Errors and Revamp
Problem: Are manual data entry and paper-based documentation costing you more than you think? Errors like misfiled documents, incorrect data entry, and lost paperwork can lead to expensive mistakes and costly rework.
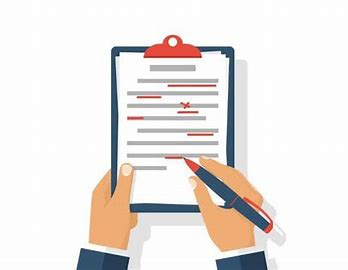
Impact: Are errors and inefficiencies cutting into your profits? Implementing quality management systems and automation can turn things around. The International Data Corporation (IDC) reports that businesses lose 20-30% of their annual revenue due to manual errors.
Solution: What if you could cut errors by 80% and streamline operations? Toyota did just that with automation, boosting efficiency and reducing rework. Automated systems deliver accurate data quickly, improving decision-making and enhancing product quality. Unlock the clarity you seek and gain valuable insights click now to delve deeper.
3. Increased Operational Expenditures
Problem: Are you underestimating the true cost of paper-based processes? It's not just about the cost of paper printing, storing, and disposing of documents all add up, impacting your bottom line.
Impact: Think paper-based processes are harmless? They can erode your profit margins significantly. For instance, General Electric saved $12 million annually by going paperless, proving the massive cost savings of digital transformation. In large manufacturing facilities with extensive paperwork, these costs can spiral out of control. Don't let paper expenses drain your profits discover the benefits of a paperless system today.
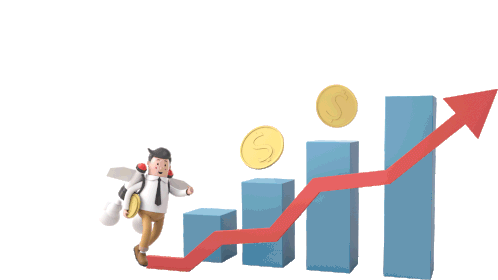
Solution: Ready to streamline your operations and boost growth? Digital records make managing data a breeze and support environmental sustainability by cutting paper waste and carbon emissions. Secure your information with encryption and access controls, and track every document change with audit trails and version control.
4. Delayed Decision Making
Problem: Still relying on paper for decision-making? Delays can be major when you're waiting for physical documents to be reviewed, signed, and returned.
Impact: Are decision-making delays stalling your production and hurting customer service? In manufacturing, waiting on physical documents can slow down production schedule adjustments and lower flexibility. McKinsey & Company found that each day of delay can shrink your annual growth rate by 3.5%.
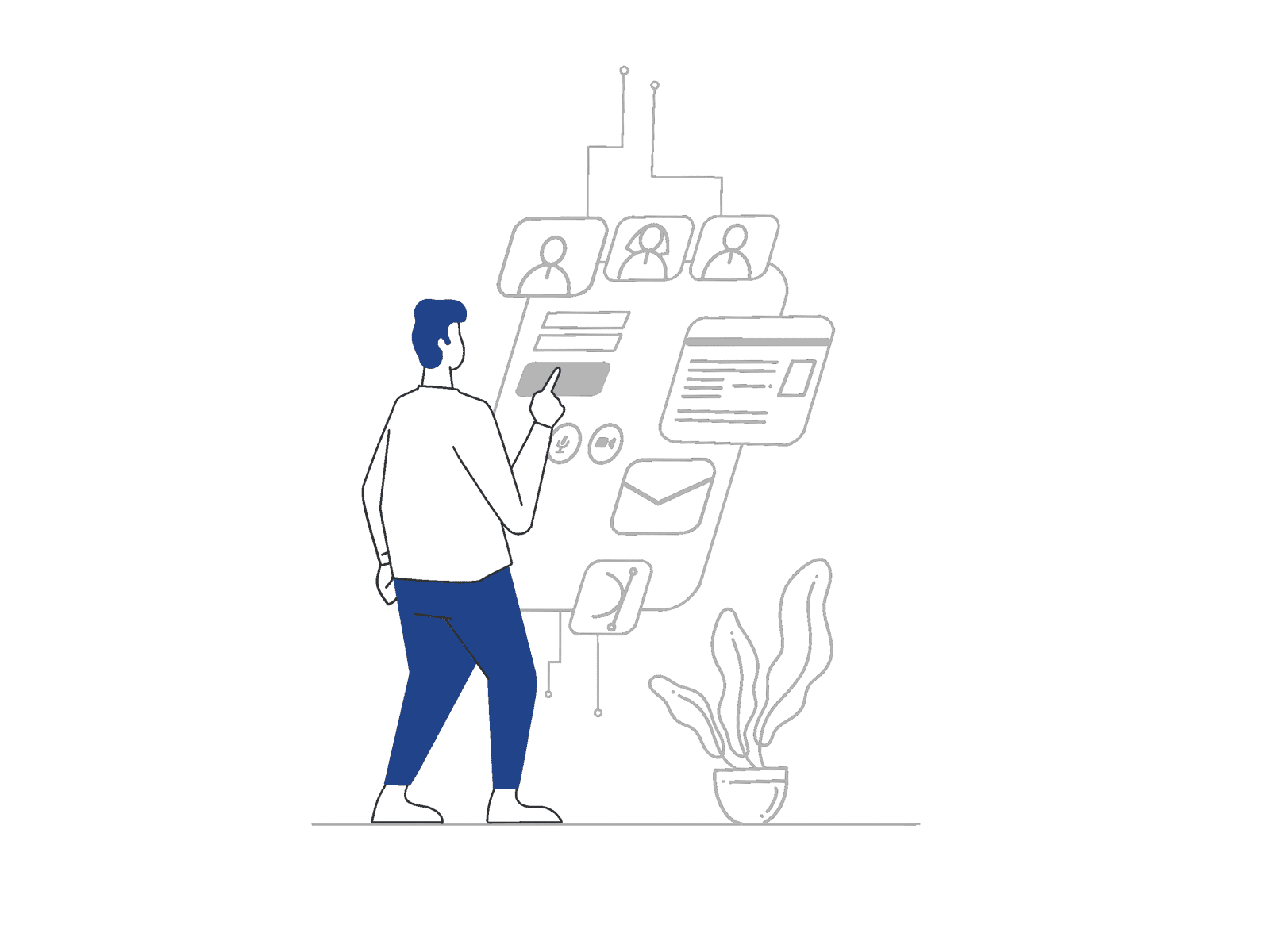
Solution: Digital workflows are a game-changer, streamlining the approval process and significantly boosting productivity. Siemens AG improved project schedules by 30% with a cloud-based collaboration platform, showcasing the impact of digital transformation.
5. Security risks
Problem: Are your physical documents at risk of loss, theft, or damage? How secure is your confidential information against disasters and unauthorized access?
Impact: Imagine losing exclusive blueprints or customer data to a security breach your business could face legal trouble, reputation damage, and financial losses averaging $3.86 million, according to IBM. In today's digital landscape, even a single breach can cripple your competitive edge and erode stakeholder trust.
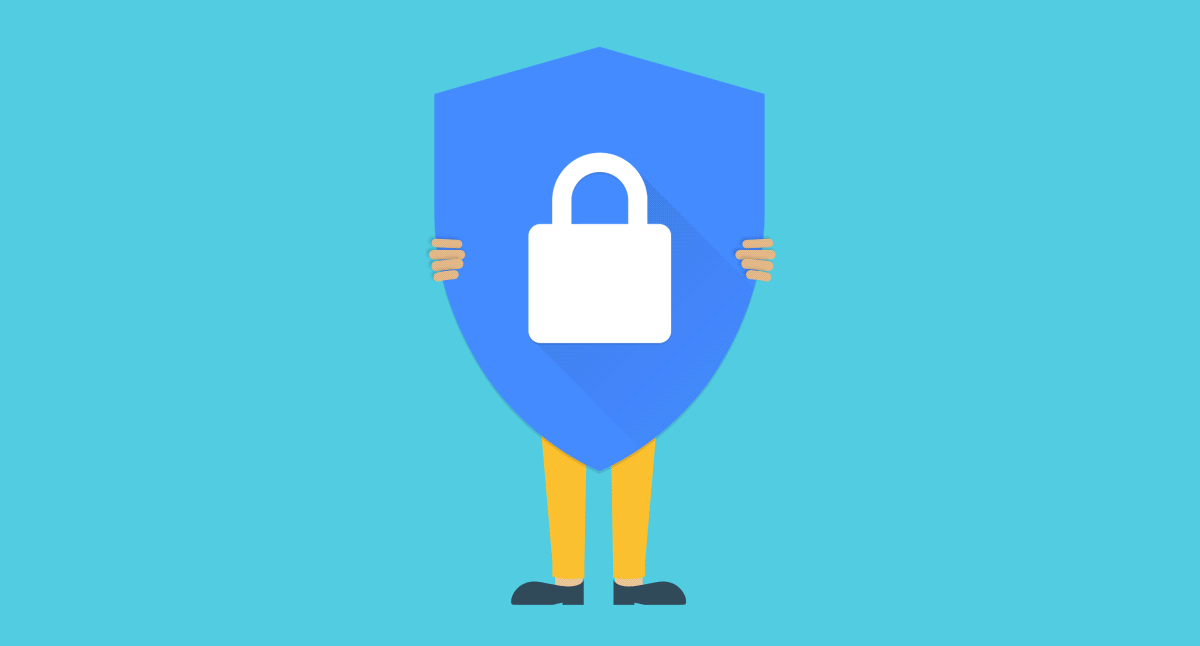
Solution: 3M s implementation of a secure digital document management system (DMS) led to a 60% drop in document-related security incidents, proving how vital a DMS is for business security. Regular backups offered by a DMS ensure that data remains accessible even during system failures, natural disasters, or cyberattacks, reducing the risk of data loss and enabling swift recovery. This not only shields against legal and regulatory risks but also builds trust among customers and stakeholders.
In today's digital economy, having a secure DMS is essential for operational continuity, regulatory compliance, and protection against evolving cyber threats. Transform the potential of your data connect with MachDatum's specialists for an exclusive demo call !!
Conclusion
Shifting from paper to digital isn't just a smart move it's a game-changer for manufacturing. At MachDatum, our QMS software and IIOT platforms are designed to deliver efficiency, cost savings, and robust security. With our scalable and configurable solutions, you can cut costs by nearly 40% and save up to 70% of your time through optimized workflows and automated processes. Imagine faster decision-making, accelerated production cycles, and the ability to respond quickly to market demands all while empowering your team and driving long-term growth. Are you ready to transform your operations and take your business to the next level?
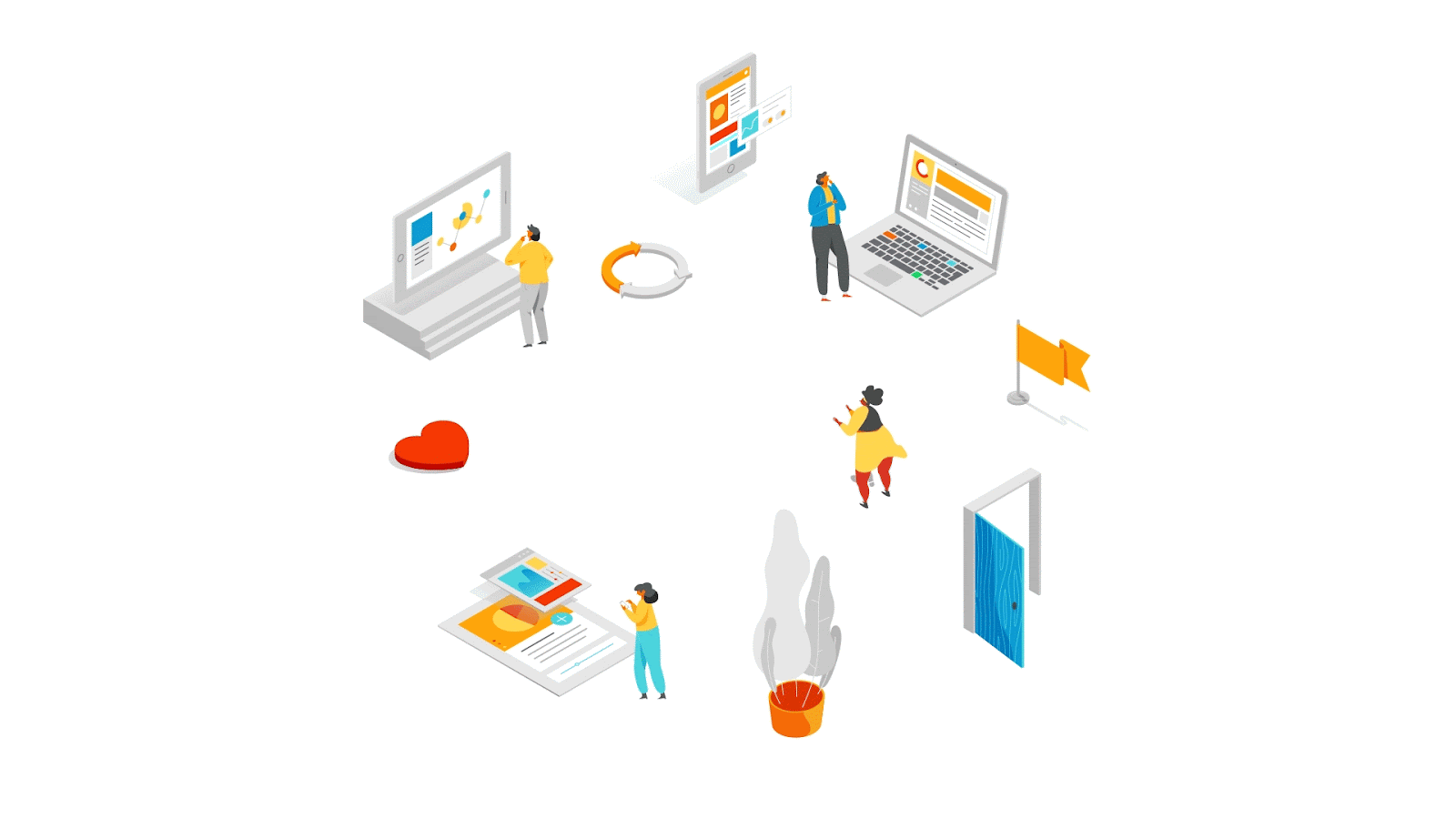